
Neocarbonix at the Core
Nanoramic’s proprietary Neocarbonix electrode technology enables battery makers to transition towards environmentally friendly manufacturing and green batteries, placing them at the forefront of energy transition sustainability. Neocarbonix accomplishes this by providing sustainable alternatives to some of the most limiting materials in conventional lithium-ion batteries and battery production – NMP solvent and PFAS “forever chemicals.”
The technology drops into existing battery manufacturing lines without impacting operations, enabling flexibility in transitioning away from the conventional NMP solvent used in lithium-ion electrode production. This allows battery manufacturers to improve worker safety, reduce electrode drying energy consumption, and improve production throughput.
Neocarbonix replaces conventional PVDF binders and additives in battery electrode slurry with a carbon binding structure. By replacing conventional PVDF, which is classified as a PFAS "forever chemical,” with Neocarbonix, battery manufacturers can set the industry standard for sustainable products. With a broad array of advantages, Neocarbonix is widely applicable across industries such as transportation, consumer electronics, stationary storage, and more.
​
​


Active
Material

Binding Additive

Conductive Additive

Neocarbonix at the Core
What Makes Neocarbonix Different?
Carbon Binding Structure
Conventional Li-ion batteries use PVDF binder like a glue to hold battery material together. They also require NMP solvent in order to dissolve PVDF during battery manufacturing.
​
Neocarbonix replaces PVDF binder with a carbon binding structure, which improves both the electric conductivity and mechanical properties of the battery. Additionally, this eliminates the need for NMP solvent, improving manufacturing worker safety. By replacing conventional battery binder and solvent, Neocarbonix unlocks a wide range of benefits for lithium-ion batteries.


Conventional
Li-ion Battery




Sustainability
A Cleaner Battery for a Cleaner Future



Safer Solvent: Neocarbonix eliminates NMP solvent and PVDF, a PFAS "Forever Chemical," from battery production. This enables battery manufacturers to prepare for potential upcoming regulations and related supply chain risks regarding NMP and PFAS while improving manufacturing worker safety.
​
Reduced Carbon Footprint: Neocarbonix reduces the carbon footprint of Li-ion battery manufacturing by 25%. This is possible by eliminating the need for NMP, which makes the drying stage of electrode manufacturing very energy intensive due to its high boiling point and low vapor pressure. By using water or alcohol solvents, Neocarbonix requires less energy during the drying stage of manufacturing and therefore emits less C02.
​
Improved Recyclability: Neocarbonix improves the recyclability of Li-ion batteries by eliminating PVDF, which needs to be broken down upon battery disassembly. Neocarbonix NMC cathodes can be designed without the use of any polymeric binder which makes them the right candidate for direct recycling. This means that the active material of the electrodes can be directly reused without hydrothermal treatment that would dissolve the active material down to its atoms first and build them up again, which is a highly energy demanding process.
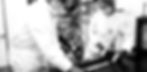
Cost
Lower Cost Through Higher Efficiency

-
Neocarbonix reduces the amount of inactive material needed to make a battery and therefore lowers material costs.
​
-
In the manufacturing process, Neocarbonix increases throughput by up to 4x on coating lines due to the higher electrode loading, saving capex and operating costs.
​
-
Neocarbonix uses solvents that dry faster than conventionally used NMP solvent which reduces operating costs.
​
-
Due to the improved recyclability, scrap electrodes can be more efficiently recycled, also allowing directly re-feeding in the production process.




New Factory

Existing Factory Retrofit


Source: Porsche Consulting Neocarbonix® Cost Report
-
When using Neocarbonix® technology with LFP cathode in a 50-kWh battery pack
-
When constructing a new 20 GWh cell factory when using Neocarbonix® technology
-
When retrofitting an existing 20 GWh factory with Neocarbonix® technology

Performance
Energy Density & Range
Batteries made with Neocarbonix have up to 35% higher energy density than conventional Li-ion batteries and therefore enable EVs with about 30% longer driving range. This allows EV drivers to make fewer stops and have the freedom to take longer trips without planning every pit stop.
​
This is possible due to Neocarbonix's high electric conductivity which allows a thicker active material layer. As a result, the whole cell needs less electrode layers to have the same energy. This also reduces the amount of inactive material (binder and conductive additives) within the Neocarbonix active layer.

Fast Charge & Power
Batteries with Neocarbonix technology have been tested to charge in less than 15 min, which is 30 min less than the market average of 45.
​
Unlike conventional batteries, Neocarbonix avoids the typical drawback of having to sacrifice between energy density and power, by simultaneously offering increased energy density and enabling fast charging through high power capabilities.

45 Minute
Charge
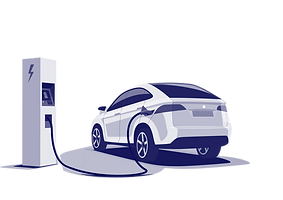


<15 Minute
Charge
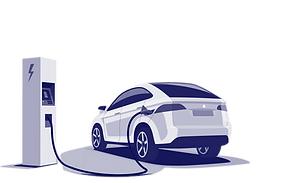


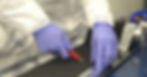
The Neocarbonix Process

Flexibility
A Drop-in Technology
Neocarbonix drops into existing battery manufacturing processes and equipment without impacting operations. This makes each of the above mentioned benefits possible without investing money or time into altering existing gigafactories.​

Enabling Next-Generation Batteries, Today
Directly Compatible with Today's Manufacturing Equipment
Drop-in Replacement for Existing Battery Technology














Conventional Manufacturing From Slurry to Cell
-
The Neocarbonix process starts with a mixture called a slurry, which contains active material, electrolyte, and proprietary Neocarbonix material.
-
Using a standard coating machine, this mixture is then cast onto cathode (positive electrode) and anode (negative electrode) current collectors, creating electrode rolls.
-
A standard calendering machine is then used to reduce the porosity of the electrode through compaction.
-
Lastly, strips of the cathode and anode are placed inside a battery cell, which comes in a variety of form factors, such as the pouch cell and cylindrical cell seen below.

Slurry

Electrode Roll

Calendering Machine

Pouch Cell